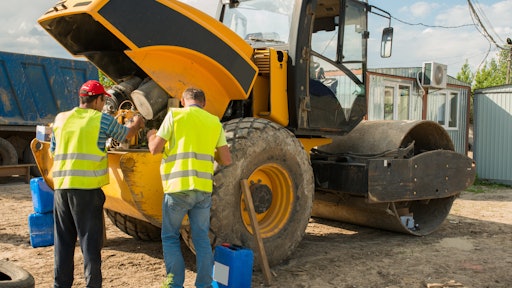
Every fleet owner should know the basics about the viscosity of the lubricants they are using and why the viscosity matters. Fleets—especially mixed ones—require a variety of lubricants. This ranges from hydraulic oils, gear oils, engine oils, and even greases. Each of these has its own viscosity. Some pieces of equipment may even require varying viscosities.
For instance, a loader may require an ISO VG 32 hydraulic oil while a crusher may need an ISO VG 46 hydraulic oil. Does it really matter if we use those grades? Yes, it matters! Using the wrong grade can affect the performance of your equipment or lead to breakdowns which directly impact the quality of work or availability of your fleet.
In this article, we will do a deep dive into understanding a bit more about the viscosities of lubricants that fleet owners usually handle as well as deciphering the need for the wide range of viscosities that exist in their fleet. We will also explore potential ways to get the “right” viscosity during challenging times.
What is Viscosity and Why Does it Matter?
For anyone who has ever seen the packaging of lubricants, the one thing that is consistent with the labeling is that the viscosity of the oil is mentioned. But why is this so important? Oil is oil, right? No, definitely not! Let’s use an example to get our fundamentals aligned.
We can start by making a sandwich. We have two slices of bread, on one side, we can spread some peanut butter. It takes a little effort to spread that peanut butter. It is a bit thick and once spread, it covers the bread completely—no bread showing at the surface. Now, if, for some strange reason, you wanted to use garlic-infused oil to spread on the other side of the bread, this would not take as much effort. The oil is thinner and once applied to the bread, we can still see parts of the bread peeking out.
Let’s relate this to viscosity. The peanut butter is more viscous than the garlic-infused oil. Viscosity is the measurement of a liquid’s resistance to flow—it takes more effort to spread the peanut butter than the oil. Viscosity can also be defined as the internal friction within the oil that resists its flow. If we turned a jar of peanut butter upside down, it would not move but the oil would. Viscosity is also defined as the shear stress (pressure) to shear rate (flow rate).
A more viscous fluid will cover the asperities on the inside of the equipment—these are the microscopic peaks on a material, similar to the pieces of bread that are exposed after applying the peanut butter or oil. However, it will take more work to move the knife over the bread to spread the peanut butter compared to the oil. While a more viscous lubricant can protect the materials, it may not be what is required by the machine.
In essence, peanut butter is more viscous than oil if we’re thinking about food-related items. Before we go further, we need to understand the various grades of viscosity that exist and how to identify them for the different types of lubricants.
The Viscosity Grades
It is very easy to get confused with the number of viscosity grades that exist, especially for fleet owners. The chart below gives a general summary of the types of viscosity grades, and it can also be used to loosely “convert” one grade into another (based on a viscosity index of 95).
Figure 1: Oil Viscosity Conversion chart from https://oilviscositychart.com/calculate/convert.php
As seen above in Figure 1, viscosity can be measured in different ways. There are two ways to measure viscosity; namely dynamic (or absolute) and kinematic.
The dynamic viscosity measures the force required to overcome fluid friction in a film and is reported in centipoise (cP) or in SI units Pascal Seconds (Pa s) where 1 Pa s = 10 P (Poise). Dynamic Viscosity can also be considered the internal friction of a fluid. This is usually used for calculating Elastohydrodynamic lubrication as it relates to rolling element bearings and gears.
On the other hand, the kinematic viscosity of a fluid is the relative flow of a fluid under the influence of gravity. Its unit of measure is centistokes (cSt) which in SI units is mm2/s, 1 cSt = 1 mm2/s. (Mang & Dresel, 2007).
Kinematic Viscosity = Dynamic Viscosity / Density
As seen in Figure 1, kinematic viscosity can be measured at 40°C or 100°C, what’s the difference? Engine oils, axle, and transmission oils are usually measured at 100°C while industrial fluid oils (hydraulics, gears, circulating oils, etc.) are measured at 40°C.
There are also different grading systems for various applications as well. Gear oils can be graded using the AGMA (American Gear Manufacturer’s Association) grade or ISO grade. Using the chart in Figure 1, it is easy to convert between the two systems.
Engine Oils – The Lower the Better?
Over the years, fleet owners may have realized that the viscosity of engine oils has been slowly getting lower compared to the 15w40 (or straight 50s) used around 40 years ago. What’s the main reason for this change? Engines have gotten smaller over time with more power.
For instance, 40 years ago, there were larger engines but with these larger engines, there were bigger lines to transport the oil around the engine. As time progressed, technology evolved, and OEMs began to create smaller engines that were more powerful. As a result, thinner oil lines were used which meant that lower viscosity oils had to be used to achieve the required pressures and flow rates.
Imagine using a straw to drink a very thick liquid like molasses. A wider straw might be able to suck up the molasses, but a thinner straw would require a lot more effort by the person drinking. If we liken that to an engine, then the pump is under a lot more strain to get the higher viscosity of oil to the parts where it needs to go. This is one of the main reasons why oil leaks usually begin at the seals around the oil pump for these engines which use the wrong viscosity of oil. Hence, lower-viscosity oils are needed for these new engines to reduce the amount of strain on the pump and get the oils to the required areas.
While a straight 50 monograde would have worked on a diesel engine 40 years ago, it simply will not provide the type of protection that a modern engine will require. This is where the advent of multigrade oils has also been able to assist in protecting the engines. On startup, a multigrade oil can move from the bottom of the sump to the top faster than that of a monograde oil which helps to reduce the amount of wear on startup.
For fleet owners, being able to consolidate engine oils can also help to manage storage and handling as well as costs (if bought in bulk). It is important to be aware of the OEM specifications and guidelines for your pieces of equipment before undertaking the role of consolidation for these oils.
Thankfully, most diesel engine oils conform to the API (American Petroleum Institute) specification which is backward compatible. This means that if an oil needs to meet a CI-4 spec, using a CJ-4 spec, within the same required viscosity grade, would be acceptable. For mixed fleets, understanding this aspect can help to consolidate the oils and possibly move to a semi-synthetic oil across the fleet which can aid in improving fuel efficiency and lowering some overall costs.
Lower viscosity oils are here to stay and fleet owners should begin the conversation with their OEMs about consolidating their fleets to make them more efficient and help in improving their overall fuel efficiency using these lower viscosity oils.
Hydraulic and Gear Oils – Which Grade Should Be Used?
Apart from engine oils, hydraulic and gear oils are the second/third most used type of oils for fleet owners. It can be a bit perplexing when the hydraulic grades run from ISO VG 15 to 32 to 68 or 100 depending on the application. Of these, the ISO VG 32 seems to be the most popular hydraulic grade, but this doesn’t mean that this grade should be used for everything!
Hydraulics are used for precision applications and need to be very clean due to the tight tolerances in which they operate. As such, it is critical that the correct viscosity is used for these types of oils. They are rated using the ISO scale which appoints a mid-range number and uses it as the assigned grade.
Each grade has a range of ±10%. For example, an ISO VG grade of 46 can be classed within this grade if it falls within the limits of 41.4 to 50.6 cSt. This is important to note especially when trying to consolidate hydraulic oils. The chart below shows different viscosity grades for the hydraulic oil, Shell Tellus S2V oil.
Figure 2: Viscosity-Temperature chart for Shell Tellus S2V
As seen in Figure 2 above, the viscosity of an ISO 15 grade hydraulic oil (Black line) at 40°C varies greatly from that of an ISO 100 grade hydraulic oil at the same temperature (Red line). For instance, at 40°C, an ISO VG 15 is 15 cSt while an ISOO VG 100 is 100 cSt. However, all the oils have a viscosity of 100 cSt but at varying temperatures, ISO VG 15 exists at 100 cSt around -3°C while an ISO VG 22 exists with this viscosity at 7°C and an ISO VG 32 exists at 15°C, etc.
As a result, it is important to understand the temperature at which your equipment is operating before selecting the appropriate viscosity grade for your equipment. Typically, this information can be found in your user manual under the lubrication section. It is also critical to consult with your OEM and lubricant supplier before making decisions on consolidating oils.
The following table gives a better understanding of the relationship between the ISO VG and the AGMA grades for Gear oils.
Figure 3: AGMA vs ISO grades for Gear oils (Viscosity Classifications, 2024)
As stated earlier, there is a range within which viscosities can be classified. As seen in Figure 3, an AGMA grade 5 translates as an ISO 220 VG. This is a very useful chart for those who may be more familiar with the ISO VG grades but receive gear lubricants that have been classified as per the AGMA system.
Can I Mix Viscosities?
Challenges can often occur within the field and there may be instances where the required ISO VG grade is simply not available—either from the supplier or the stock room. Can another grade be used instead? In these instances, people often tend to switch to a heavier grade of oil hoping that it will still offer the protection that they need without compromising the efficiency of their equipment.
But does this mean that the entire sump must be drained before adding this heavier viscosity? Or what will the new viscosity be with these two viscosities now co-existing in the sump? This is where the Widman viscosity calculator really adds some value.
This calculator allows operators to enter the viscosity of the two oils to be mixed as well as the percentages of their mixture and of course their operating temperatures. With this information, one can easily calculate the resulting viscosity.
For the first example, if our sump had an ISO 68 oil in it and we needed to top up the oil but there were no more ISO 68 oils available, what could we do? If an ISO 46 oil was available, then we could potentially top up with this oil to achieve the required viscosity. But how much oil would we need?
We can use the calculator to find out. In this case, I placed the ISO 68 sump at 70%. This resulted in a value of 60.32 cSt which is just outside of the ISO 68 range of 61.2 – 74.8 cSt:
Figure 4: Mixing of two oils (ISO 68 @70%)
In this case, we cannot top up with 30% of the ISO 46 oil.
Let’s try for a sump size of 80% instead which results in a viscosity of 62.76 cSt which barely falls within the ISO68 range (61.2 – 74.8 cSt):
Figure 5: Mixing of two oils (ISO 68 @80%)
If, however, we used a top-up of 10% of the ISO 46 oil, we fall a bit closer within the range with a value of 65.32 cSt.
Figure 6: Mixing of two oils (ISO 68 @90%)
In this case, the top-up of 10% will keep our equipment running within the required viscosity until we can procure an ISO 68 oil for our machines.
One must note that when mixing oils, OEMs should be consulted. It is also critical to stay within the same “family” of lubricants as this increases the likelihood of compatibility between the two mixtures. It is NOT advised to mix lubricants of different brands or families (gear oil with hydraulic oil) as there may be incompatibilities that can negatively impact your system.
Understanding and assigning the correct viscosity to your equipment is just one step on your journey toward achieving greater efficiency and reliability for your fleet. The viscosity of a lubricant is important and can affect your productivity directly if not taken seriously. Let viscosity be your guide in achieving lubrication excellence for your fleet.
References
Mang, T., & Dresel, W. (2007). Lubricants and Lubrication. Weinheim: Wiley-VCH.
Viscosity Classifications. (January 27, 2024). Retrieved from tribology-abc.com: https://www.tribology-abc.com/abc/viscosity.htm